18
[this is the first article of a two-part series. The second article can be seen here]
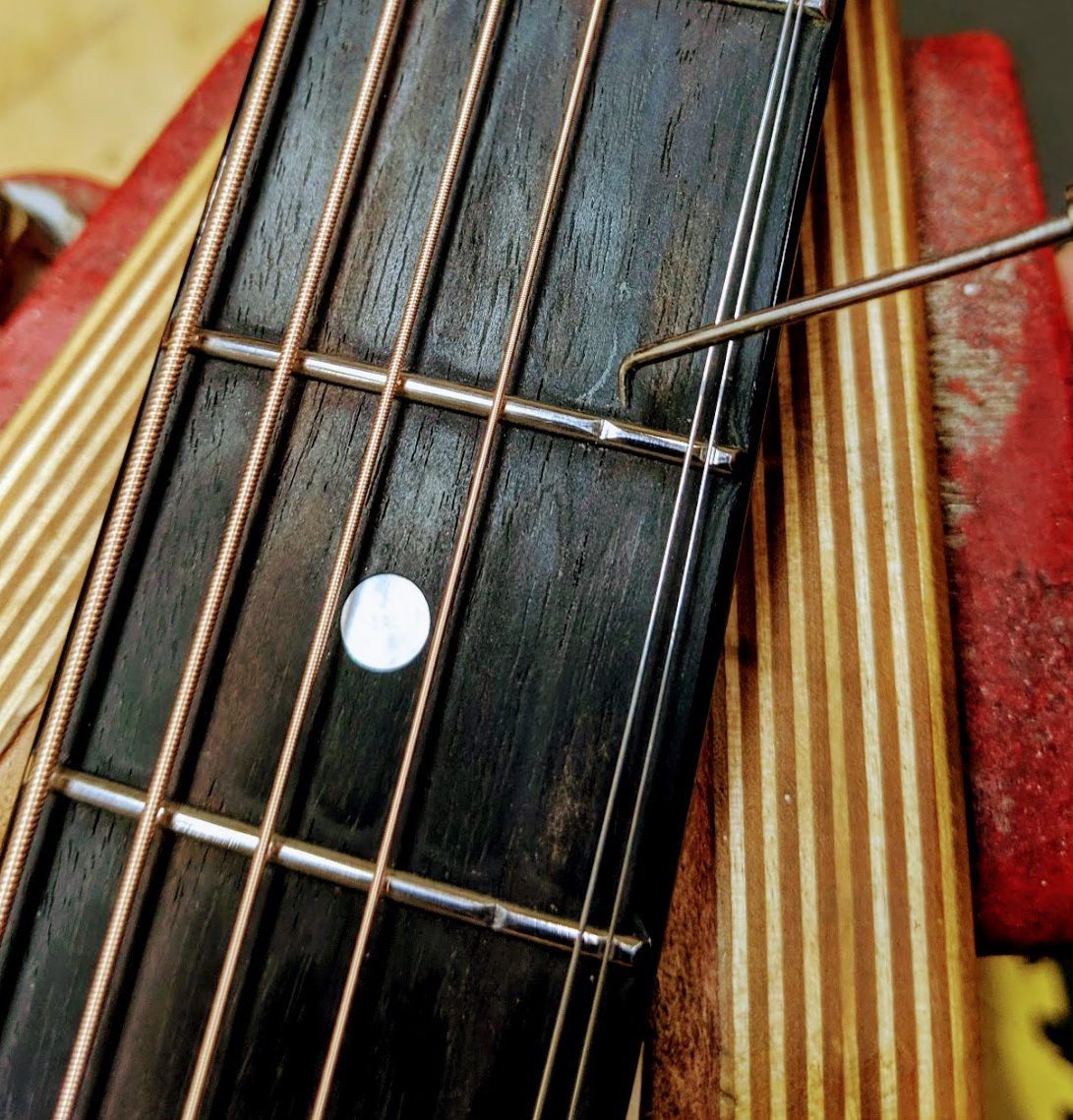
A recent Martin refret provides a great backdrop to discussing what makes desirable in fretwork for the guitar player. This articles focuses on fret issues along with what a player desires in good fretwork. In a second article, I share my process for producing excellent frets and a well-playing guitar .
What Musicians Desire in Great Fretwork
Often guitar players may not realize their frets are responsible for less than desirable playing. After all, guitar players are used to the way their guitars play. As the frets slowly worsen, the playing experience degrades little by little, the guitarist becomes the proverbial frog in the boiling pot. Inevitable fret wear, humidity, and original construction approaches are all possible contributors.
Worn or uneven frets present three possible outcomes:
- Intonation issues: fret wear causes the string to fret forward of the fret crown peak, shortening the string length and causing sharp notes.
- Fret buzz: a fretting a string on a significantly worn fret can lower the string such that the next fret (with less wear and more height) makes contact with the string when struck. High frets resulting from inconsistent fret installation or loose frets are also buzz producers.
- Difficulty playing: fretting strings over inconsistent fretwork causes muted notes and left-hand fatigue. Often excessive neck relief (too much bow) and high saddle height compensate for inconsistent fretwork (more space under the strings reduces the likelihood of buzzing.)
As musicians, what would we like from our frets? Primarily three attributes:
Accurate frets – Properly installed, fully seated, and crowned at the exact same height. Accurate frets are the foundation for a well set up guitar.
Comfortable left-hand play – When frets are accurately installed, the string height at the nut can be minimized, making fretting on the first several frets far easier. Neck relief (neck bow) can be reduced, improving mid-neck string feel and reducing fretting effort. Finally saddle height can be reduced, improving upper register fretting.
Durability and stability – Selection of fret material directly relates to wear. While most guitars come with nickel frets, two longer lasting materials are available.
- Evo wire, with a gold-colored hue, tends to last 50% longer than nickel. It’s formulation adds 20% zinc in place of copper for greater wear resistance.
- Stainless steel frets can also be installed, which often last the life of the guitar with no need for replacement.
Both of these alternate materials are more expensive to install, but return value on far less frequent fret work in the future. Finally for stability, frets should be glued in place during installation. This helps ensure a lack of fret movement, thereby not introducing high frets (and fret buzz) over time.
The next article, The Road to Great Frets, shares the fret installation and setup process which achieves the above attributes.